Industry news
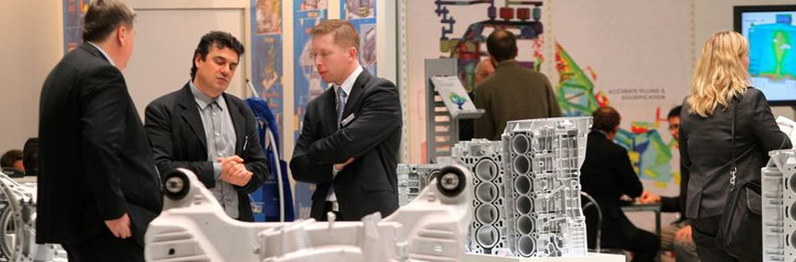
The die-casting industry has been fully integrated in the further societal and technological development. In this, the automobile industry, which buys 80 % of the die-cast parts production, plays an important role [1 and 2]. The trend away from the combustion engine and towards alternative drives has inevitable effects on the demand for die-cast parts: While a combustion engine contains approximately 220 of those parts, only about 25 – that is, only one tenth of them – are needed for an electrical drive. Changes in the mobility behaviour of people such as car sharing, the use of robocabs or autonomous driving [3] could have the additional effect that far less vehicles and thus far less crash-proof components are required.
Nevertheless, die-casting foundries can be optimistic about the future because for each vehicle components such as structural components or sensor casings, which satisfy strict specifications and can be produced cost-effectively by die-casting, will continue to be necessary. Also electric motors require die-cast parts such as battery housings.
Networks and Partnerships
Modern die-casting foundries are accustomed to manufacturing demanding parts and meeting economic challenges: "Many companies", says Gerd Röders, CEO of G.A.Röders GmbH & Co.KG and President of the German Die Caster's Association VDD, “have been engaged in material-sciences for a long time. Therefore, the die-casting technology has developed strongly with regard to alloys, production processes and application possibilities. Nowadays, it is possible to produce die-cast parts which are weldable and can be glued or riveted. At the same time, procedures are available in order to finish the surfaces according to the application. All this was unthinkable a decade ago”. Such parts, which incorporate a lot of development effort, meet the requirements of demanding customers with regard to criteria such as light weight design, strength and crash behaviour (Fig. 1).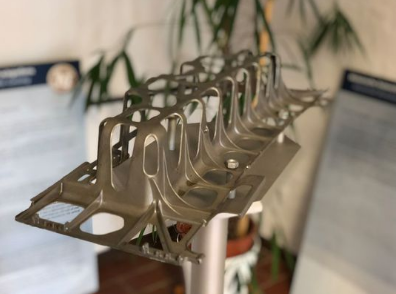
Also internal processes in die-casting foundries have changed: In the past, it was normal to manufacture parts purely according to drawings; today, companies such as the family-run Röders company with a staff of approximately 400 are integrated via simultaneous engineering in development processes of the customers right from the start.
Another strength is that the companies – at least in the German-speaking regions – are integrated in well-established networks. Together with universities which carry out applied research and companies which are specialized in complementary technologies, project-based partnerships can be formed quickly.
Cost Saving Potentials
European die-casting foundries operate under high pressure to perform and to act cost-effective which is increased by the competition with other materials such as steels and plastics, the shifting of market places towards East Asia, and the growing influence of Chinese market participants as well as their market and business strategies. Particularly in those countries where energy and labor costs are high, this pressure can be lowered by using modern die-casting machines that are practically available around the clock and economical in terms of raw material and energy consumption. The trend is moving towards an increased material efficiency, i.e. a production with a scrap rate which goes to 0 %. For Marcello Fabbroni, Head Marketing & Product Management Die Casting of the Swiss-based manufacturer of die-casting machines Bühler AG, improving cost efficiency is a huge potential for optimization, and he points to in-house activities: „At Bühler AG, with respect to new developments we pay attention to the topic 30/30, that is to say that with new projects we try to reduce 30 % waste and to reduce 30 % energy. For all development projects these goals must be taken into account in the specifications”. Also the topic of digitization (Industry 4.0) is of growing significance because by means of digital technologies, processes can be controlled more efficently and optimization potentials can be better recognized. Furthermore, production data can be clearly and comprehensively documented. This is becoming more and more important regarding responsibility matters.Citation
引用[1] Global Automotive Supplier Study 2018. Roland Berger GmbH, München, Dezember 2017.
https://www.rolandberger.com/de/Publications/pub_global_automotive_supplier_study_2018.html
[2] The Future of the Automotive Value Chain: Supplier Industry Outlook 2025. Deloitte Consulting, Dezember 2017.
https://www2.deloitte.com/de/de/pages/consumer-industrial-products/articles/automotive-value-chain-supplier-industry-outlook-2025.html
[3] Robocabs – Taxi-Roboter auf dem Vormarsch. auto.de, Oktober 2017.
http://www.auto.de/magazin/robocabs-taxi-roboter-auf-dem-vormarsch/
Tags: Die-Casting , challenges , Bühler , Structural component , automobile , industry , euroguss , digitization , 4.0